Products
- Metal Casting
- Die Casting
- Sand Casting
- Gravity Casting
- Investment Casting
- Non Ferrous Casting
- Metalworking Service
- Metal Fabrication
- Sheet Metal Fabrication
- Metal Welding
- Metal Cutting
- Metal Bending
- Metal Plate Rolling
- Metal Roll Forming
- Metal Stamping
- Deep Drawn Stamping
- Expanded Sheet Metal
- Metal Perforating
- Plastic Molding
- Injection Molding
- Rotational Molding
- Blow Molding
- Thermoforming
- Precision CNC Machining
- EDM Machining
- Heat Treatment
- Surface Treatment
Sand Casting
Sand casting also called sand mold casting, it's used to produce a wide variety of metal components with complex geometries. These metal parts can vary greatly in size and weight, ranging from a couple ounces to several tons. The small sand cast parts include as gears, pulleys, crankshafts, connecting rods, and propellers. The larger sand casting applications include large equipment housings or heavy machine bases. Sand casting is also common in producing automobile parts, such as engine blocks, engine manifolds, cylinder heads, and transmission cases.
Suitable material: Ductile Iron (SG Iron/Spheroidal Graphite Iron), Grey Iron, Cast Steel, Aluminum, Brass:
We provides a high quality affordable solution for metal casted products according to customer requirements. We are able to utilize our low cost structures in China, and provide a low cost and reliable final product, lower than almost any other countries sand casting manufacturer.
Green Sand Casting
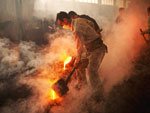
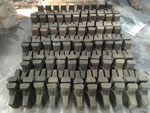
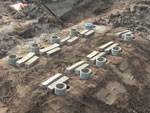
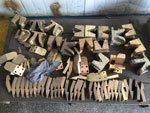
Green sand casting is the most widely and most convenient method of sand casting. It has the advantages of low cost, flexibility, high productivity, short production cycle and etc. With approximately 60 - 70% usage of all sand casting. Green sand casting is cheaper than resin bonded sand casting.
Resin Bonded Sand Casting
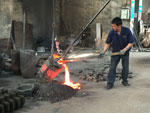
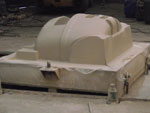
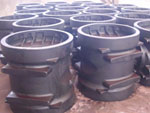
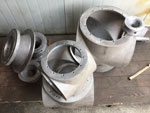
The resin bonded sand as a barrier in the casting production. It can effectively prevent the sand sticking on the cast parts. And it can removed nitrogen, sulfur and other gases. So it can guarantee the quality and stability of cast parts.
Shell Mold Casting
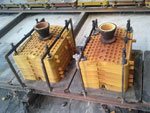
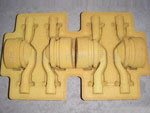
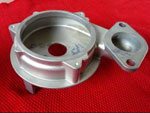
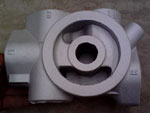
Shell mold casting process offers better surface finish, better dimensional tolerances, and higher throughput due to reduced cycle times. The materials that can be used with this process are cast iron, grey iron, ductile iron, carbon steel, stainless steel, alloy steel, aluminum, aluminum alloy etc. We provide OEM services and have a team of experienced engineers.
Lost Foam Casting
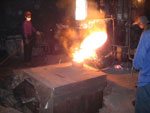
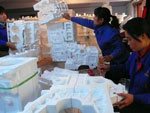
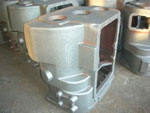
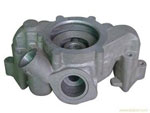
Advantages of Sand casting (Sand Mold Casting):
1. Can produce very large metal parts
2. Can form complex shapes
3. Many material options
4. Low tooling and equipment cost
5. Short delivery times
Ductile Iron Casting (SG Iron, Spheroidal Graphite Iron)
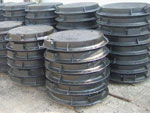
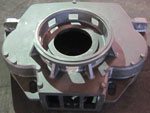
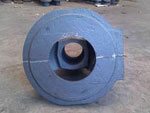
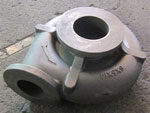
Grey Iron Casting
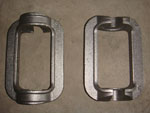
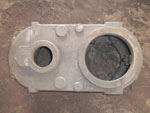
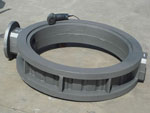
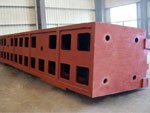
Cast Steel Casting
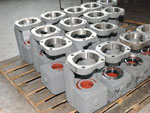
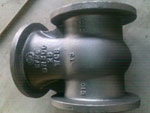
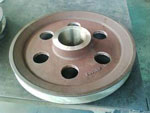
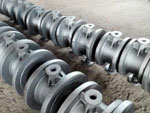
Aluminum Sand Casting
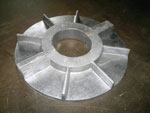
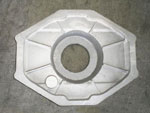
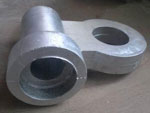
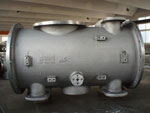
Brass Sand Casting
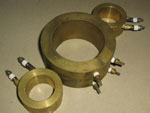
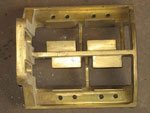
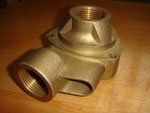
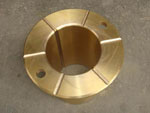
Maxtech is a professional sand casting foundry in China. We offer a reliable and low cost sand casting solution, such as: green sand casting, resin bonded sand casting, shell mold casting and lost foam casting.
The main sand casting material has iron (grey Iron, ductile Iron, S.G. Iron), brass, aluminum, steel and etc.
We support technical standards of metal casting, includes: ASTM, ANSI, SAE, DIN, and BS.
We also provide the following services:
1. Metalworking Service, CNC Machining and EDM Machining Service
2. Heat Treatment:
Hardening, Annealing, Normalizing, Stress Relieving, Softening, and Graphitization
3. Surface Treatment:
Metal Polishing (Metal Mirror Polished, Brushed Metal Finishing), Shot Blasting, Sandblasting, Spray Painting, Powder Coating, Thermal Spraying, Anodizing, Chrome Plating, Nickel Electroplating / Electroless Nickel Plating, Hot-Dip Galvanizing, Copper Plating, Phosphorizing, Electrophoresis and Passivation
4. Assembly
5. Packing
6. Testing Report, QC Report